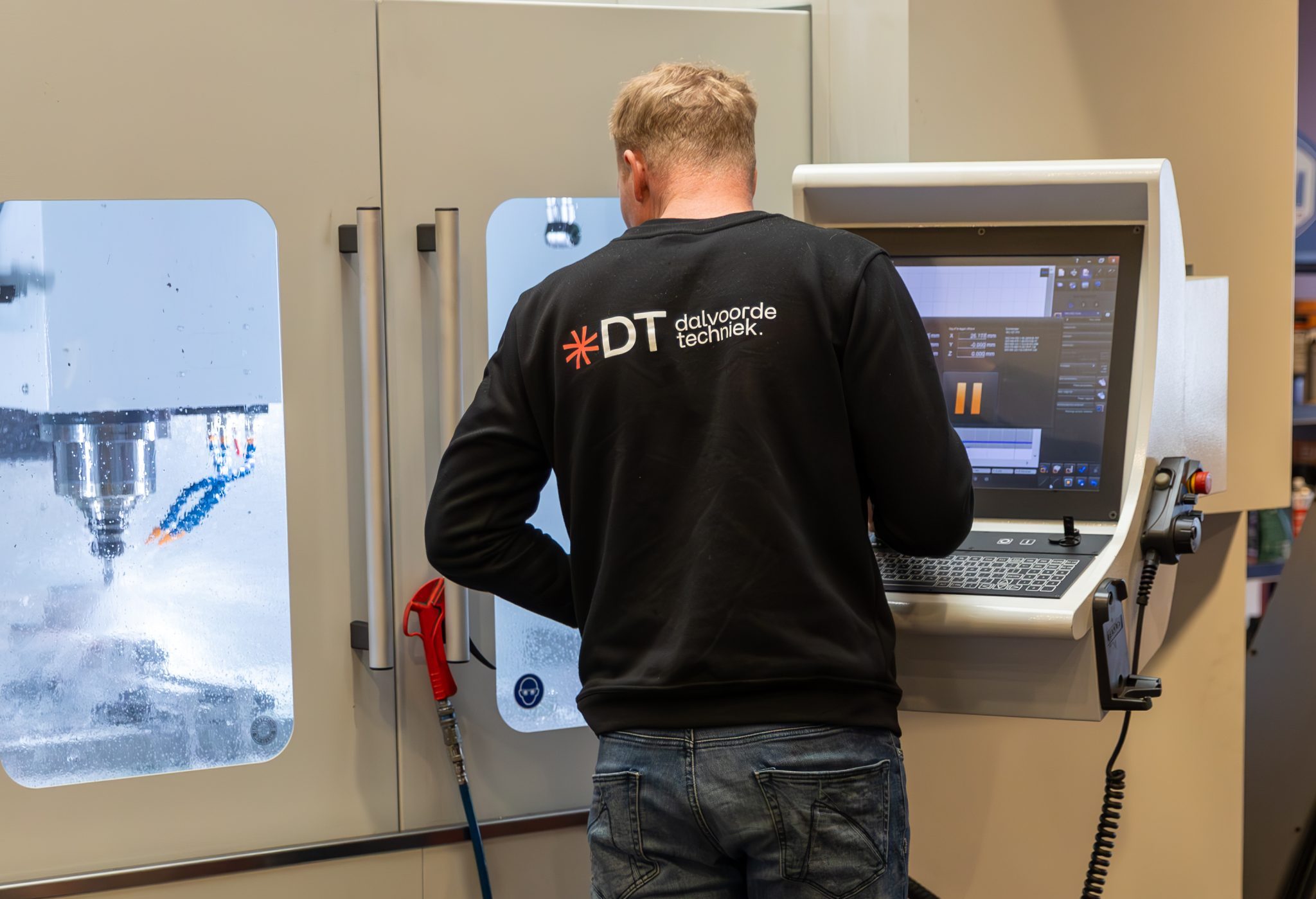
Machining
At Dalvoorde Techniek, we specialize in precision machining. Whether it is CNC turning and milling or repairing parts, we deliver the highest level of accuracy. Trust us with your project, whether it is a single piece, small series, or urgent orders. With our advanced machinery and experienced team, we are always ready to meet your needs.
- 24/7 Emergency CNC Machining
- Quick Delivery Times
- Materials: Steel | Stainless Steel | Brass | Plastics
Our Machining Services
Our advanced CNC machines ensure efficient and precise machining. We understand that speed and accuracy are crucial in your production processes. That is the reason why we are ready to meet all your machining needs with the highest standards of precision and efficiency.
• Turning and Milling: Both CNC and conventional machining
• Boring: For precise boring operations
• Keyway Broaching or Shaping: For accurate keyways and splines
• Reconditioning Services: : Repair and optimization of parts
• 24/7 service: We are always available for urgent machining requests
• Custom Measurements: Available in both metric and imperial units
CNC Machines at Dalvoorde Techniek
At Dalvoorde Techniek, we operate a variety of CNC machines in our workshop in the Netherlands, ensuring precise and efficient machining. Our Style CNC turning and milling services cater to a wide range of needs, from single-piece productions to custom parts for any project. Our equipment includes the STYLE 510 lathe and the STYLE MC 1000 milling machine, both designed to deliver exceptional accuracy and reliability.
CNC Lathe / Milling Machine
The STYLE 510 CNC lathe is designed for precise CNC turning of metals. With a turning diameter of up to 510 mm over the bed and 300 mm over the carriage, and a distance between centres of 1850 mm, we can efficiently turn a wide variety of metal parts. This machine is ideal for creating prototypes, single parts, and small series. It also features a 102 mm bore, offering additional flexibility for various applications.
The STYLE MC 1000 milling machine provides powerful milling capabilities, with a stroke of 1000 mm on the X-axis and 510 mm on the Y- and Z-axes. This machine operates at up to 12,000 rpm, making it ideal for CNC milling of both large and complex components.
Need a reliable partner for your projects?
Get in touch directlyEverything you need to know about machining at Dalvoorde Techniek
Machining is a crucial process in metalworking, where excess material is removed from a workpiece to create parts with the desired shape and dimensions. At Dalvoorde Techniek, we have extensive experience with a wide range of machining techniques. Curious about the diverse projects we have completed? Visit our projects page
Call us!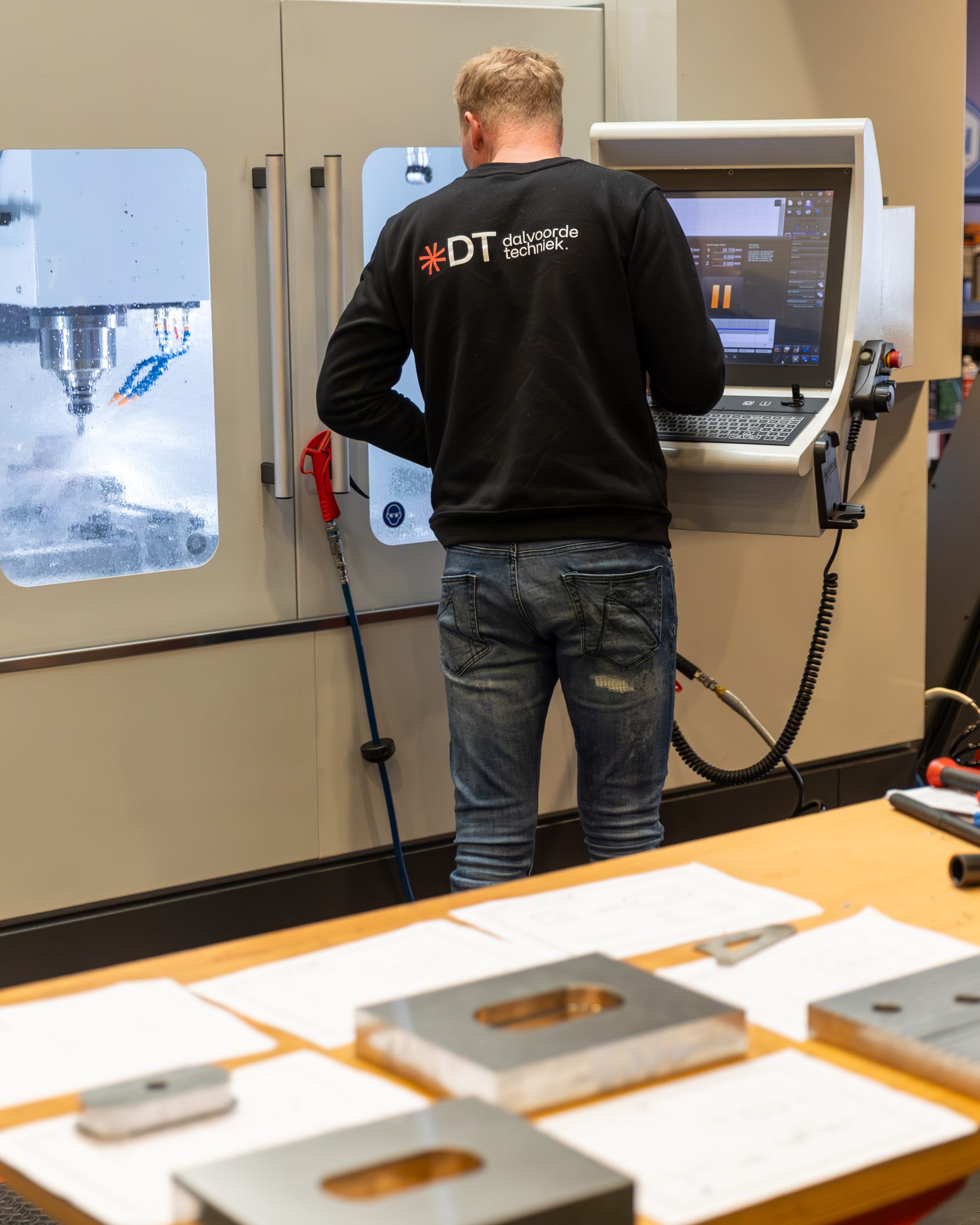
Turning vs. Milling: What's the Difference?
During turning the workpiece rotates rapidly on a lathe, while a cutting tool removes material. This technique is ideal for creating cylindrical and round shapes, such as shafts, rings, and tubes. By CNC turning the workpiece, we can produce precision parts like motor shafts and fastening rings, ensuring accurate shapes with continuous rotation.
Milling , on the other hand, works differently. The cutting tool rotates rapidly while the workpiece remains stationary. This method is perfect for creating complex shapes and profiles, such as cutting grooves, manufacturing gears, and working on flat surfaces with detailed patterns. Milling is excellent for precise adjustments and prototyping.
Examples:
• Turning: To manufacture a motor shaft that needs to be precisely round and to size, we use turning to achieve the desired diameter and accuracy.
• Milling: For a metal housing with complex cut-outs and patterns, we use milling to create the exact shapes and details.
Curious about what we can turn and mill in our workshop? Feel free to call or email us.
CNC vs. Conventional Machining?
CNC Computer Numerical Control, machining involves turning metal on a lathe or milling metal on a milling machine using computer-controlled machines. These machines operate with extreme precision, allowing the production of repeatable and complex parts. CNC is ideal for producing large series or custom parts with strict tolerances.
Conventional turning and milling are performed using manually operated machines. This method is suitable for single items or small batches. It includes standard machining techniques such as filing, planing, tapping, broaching, boring, sawing, and drilling. Conventional machining is often more flexible for small series or special adjustments but may be less precise than CNC. We combine both techniques to ensure the best quality for every project, large or small.
Examples:
• Repairing an old machine part with unusual dimensions and shapes, where conventional turning or milling provides the best solution.
• Creating a custom tool or mold for a one-time project, where conventional turning and milling is often more cost-effective and faster than CNC machining.
What is Boring?
Boring and large boring are important machining processes where the workpiece remains stationary, and the tool rotates
These techniques are mainly used for repairing holes in metal products. When a round hole becomes damaged, worn, or deformed, the boring technique can be used to restore it to the correct round shape.
Boring uses a fast-rotating cutting tool to precisely machine the stationary workpiece. Unlike CNC turning, where the tool is directed inward, the boring tool is oriented outward in this process.
Key machining techniques: keyway cutting and broaching
Keyway cutting and broaching are machining processes often used to create specific grooves or profiles in workpieces.
Keyway Cutting:
Keyway cutting is a machining process where a narrow, straight groove is created in a shaft or hub. This groove is designed to accommodate a key, which ensures a secure connection between two parts, such as a shaft and a gear. It prevents the parts from rotating relative to each other. A common example of keyway cutting can be found in machine drive systems, where it is essential to securely connect gears and shafts.
Broaching:
Broaching is a technique used to create internal profiles, such as keyways, but also other shapes like square or hexagonal holes. This process uses a specialized tool called a broach, which is either pulled or pushed through the workpiece. The broach features multiple cutting edges that remove material layer by layer until the desired shape is achieved. A practical example of broaching is creating internal square holes in wrenches or forming keyways in gears.
Which materials are suitable for machining?
- Plastic: Versatile and lightweight materials like nylon and PTFE, ideal for components requiring chemical resistance.
- Steel: Strong and durable, perfect for creating robust parts that need to withstand heavy use.
- Stainless Steel: Corrosion and rust-resistant, making it ideal for parts exposed to harsh environments.
- Aluminium: Lightweight and easy to machine, commonly used in applications where weight is a crucial factor.
- Brass: Easy to machine with a good surface finish, frequently used for precision parts such as valves and gears.
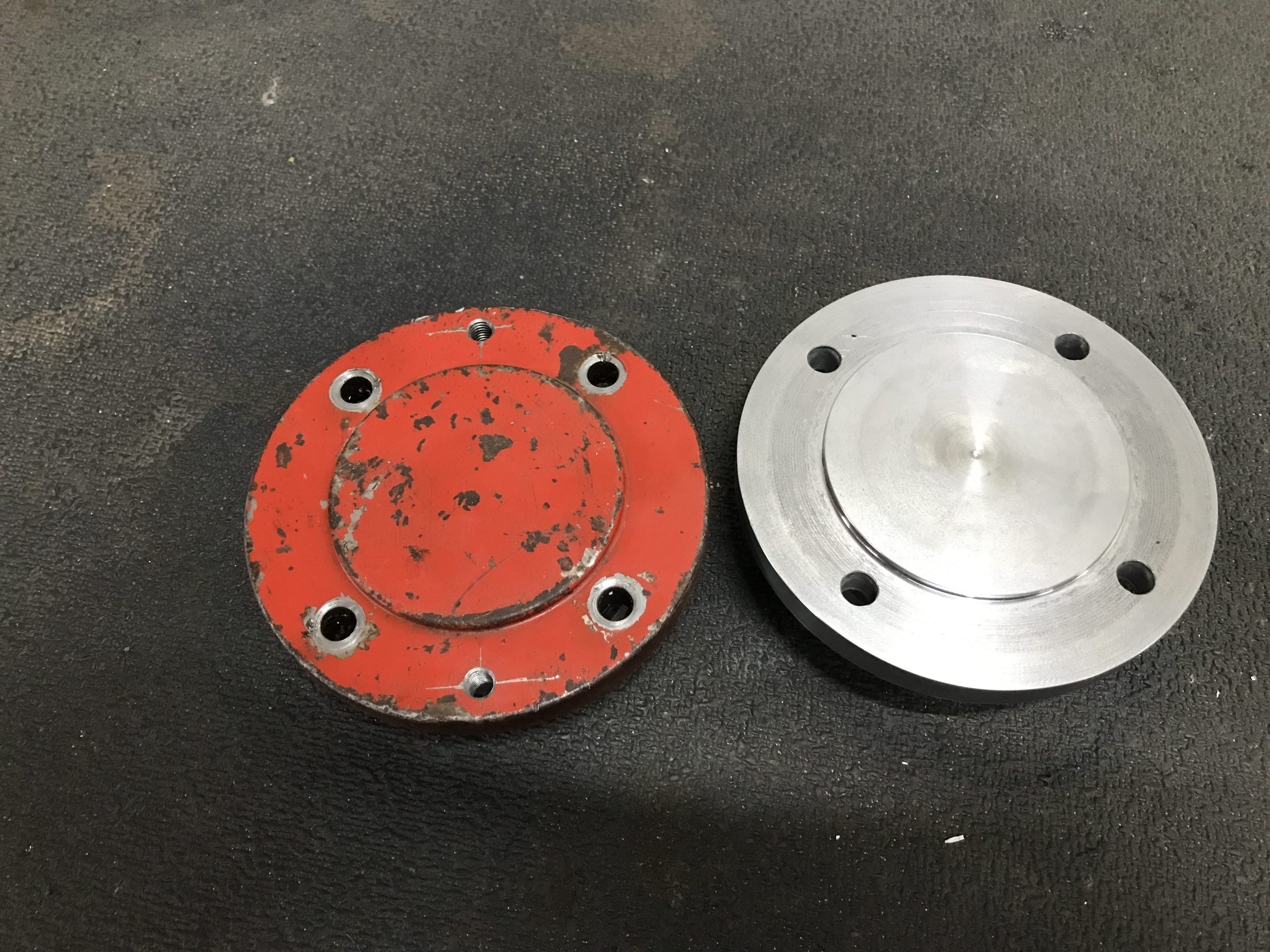
Let’s talk!
Interested in what we can do for you?